Ihre Ansprechpartner

Walter Fichter
Prof. Dr.-Ing.Direktor
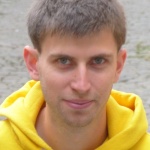
Torbjørn Cunis
Dr.Akademischer Rat auf Zeit / Gruppenleiter Aerospace Control Systems & Optimization
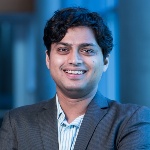
Aamir Ahmad
Jun.-Prof. Dr.-Ing.Stellv. Institutsleiter
Direktor
Akademischer Rat auf Zeit / Gruppenleiter Aerospace Control Systems & Optimization
Stellv. Institutsleiter